日期:2017-04-10 / 人气: / 来源:www.biglss.com / 热门标签: 精益管理
欢迎您访问博革咨询凯发app官网!博革咨询是中国首家整合精益生产/六西格玛/流程再造的咨询公司,专注于提供 精益生产、6s现场管理、tpm设备管理、精益工厂布局、专业目视化、精益供应链、精益研发、六西格玛管理、智能制造等综合性问题凯发app的解决方案并负责落地实施。
全国咨询热线:021-62373515、157-2153-3189
我们承诺:见效快、易复制,目标必对赌!
精益管理中解决问题的六大步骤:
一、描述问题。
这是关键的一步!按照如下方案实施这一步骤:
用书面陈述描述问题。好的问题陈述描述了您自己的经验和可衡量的术语。了解工作的基本流和瓶颈。
陈述应该:
明确—它是什么,它不是什么?问题有多严重?
时限—他第一次出现是在什么时候?
当前—问题目前的趋势是什么?它是在增加、减少或者保持不变?
二、实施临时性的限制对策。
如何防止客户(内部的或者外部的)受到这些问题的影响(额外的检查、额外的操作等)?
实施合适的保护方案(这是临时性的限制措施)。
分析问题和制定可能的凯发app的解决方案。
既然已经确定了问题,那么下一步是仔细分析问题的时候了。
三、搜集问题的资 料。
使用分析工具,确定至少3个可能的原因。如果可能,使用标准检查,发现凯发app的解决方案;研究是否可以实行最佳方案。(如果您只能确定一个可能的原因,那么您很可能已经发现问题的真正根源。)
分离您所发现的额外问题。(在分析阶段发现的单一问题往往后来被证明是由多个问题组成的。)
对于每个可能的原因,制定至少两个可能的解决
方案。(考虑对客户的可能影响—安全、成本等)
转至步骤4.
在这些方法中,也许最有效的是在下一页列出的4-m核对。
另一种有效的工具是3m;浪费、过载和不均衡。
常见的分析工具
·4m:人员、机器、材料、方法
·3m:浪费、过载、不均衡
·3现(现场、现物、现实)、3不(不合理、不均衡、不一致)
·流程图、因果图、核对列表、排列表、图、柱状图、5w1h
用于潜在凯发app的解决方案的典型工程
·头脑风暴
·标杆学习
·亲和图
四、确定根源和选择凯发app的解决方案。
a.使用5个为什么分析,测试每个可能的根源。对于要解决的每个问题,连续问5次“为什么”该情况会存在。
b.选择最可能的根源(造成5个为什么的可能原因)。
c.说明拟定的凯发app的解决方案受到什么制约(需要批准、时间、资本和对其它方的影响等),了解是否由于这些制约是某些凯发app的解决方案无法实施。
五、实施凯发app的解决方案。
对实施行动计划达成一致(特定的步骤、谁实施各步骤,以及何时和怎样实施)。
在进行实施时,与重要的决策者取得共识。受凯发app的解决方案影响的每一个人都要参与。
根据实施计划,监测和显示进展。
六、验证凯发app的解决方案的有效性
搜集问题的资料,使用监测系统和衡量方案,已确定是否取得了改进。
已经消除问题了吗?发现并解决根源了吗?如果已经做到,准备工作说明书、流程图或者其它文件,确保凯发app的解决方案实现标准化。检查并了解是否工厂的任何其它领域也可以从凯发app的解决方案中获益,并和他们分享信息。
如果没有做到,数据有改进吗?您的凯发app的解决方案可能不足以消除真正的根源。或者您对问题的根源判断有误,或者采用了一个并不充分的凯发app的解决方案。
这些数据保持不变—或者变得更糟了吗?在这种情况下,您的凯发app的解决方案并没有找到问题的实际原因。
如果没有取得令人满意的进展,或者问题没有被消除,返回步骤1!
作者:博革咨询
咨询采购表
精益生产怎么做?六西格玛咨询怎么做?项目周期是多少?大概需要多少费用?
我是什么企业?目前需要解决的问题是什么?预算周期是多少?想要达到什么效果?
欢迎您浏览博革咨询官方网站!我们专注于精益生产咨询、六西格玛咨询、精益供应链咨询、5s6s现场管理、tpm设备管理咨询、工厂布局规划、目视化看板设计等领域的落地咨询;若对本页面内容不感兴趣或想了解更多与您企业、行业相关的资讯,可通过以下方式寻找解决方法:
(1)工作时间可拨打我们的全国咨询热线:15721533189,021-62373515 进行咨询;
(2)在网站栏目右侧“搜索框” 输入您感兴趣的关键词,搜索相关内容;
(3)点击左侧“在线咨询”按钮, 您可以和我们的专家老师在线咨询;
(4)非工作时间请点击网站下方的“留言” 按钮,留下您的凯发app的联系方式和需要咨询的内容,我们将安排专业顾问给您解答;
(5)入群方式:扫描左图二维码,添加小博微信好友,通过认证后,加入精益生产vip会员微信群。
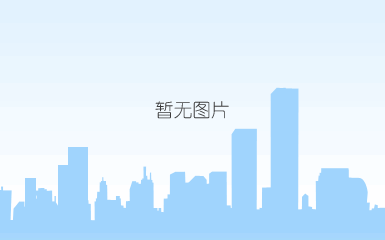
热销课程 hot
相关内容 related
- 精益管理有哪十大工具?12-03
- 什么是均衡化生产?11-28
- 5why分析法的经典案例11-13
- twi-ji推进方法11-06
- 工厂管理的二十八条浪费10-26
- 什么是生产管理七大浪费?10-12