一、项目推进总体思路
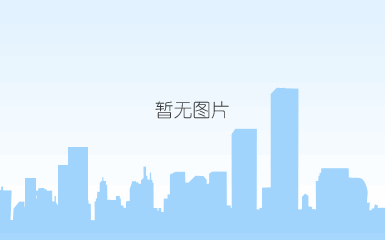
采用以下的精益化管理推进总思路,项目分两个阶段实践和探索,重点放在综采生产效率、连采掘进效率、 队伍建设等方面。
第一阶段:选定一个矿场推行精益化管理,主要在综采生产管理方面开展了“3 x”柔性检修、生产组织优化等内容,收到一定效果;
第二阶段:完善体系、优化作业流 程、细化生产调度指挥、完善连采掘进管理等内容;
二、综采效率提升
1)数据分析--确定关键绩效指标:
►开机率 = 实际运行时间/计划生产时间
►负荷率 = 实际产出/理论产出
►oee(设备效率) = 开机率 * 负荷率
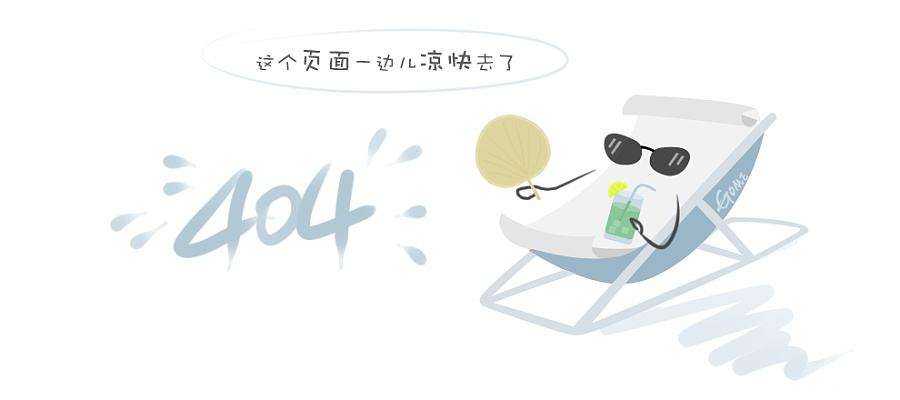
2)制定方案--目标分解,提升系统oee
以oee指标为引导,制定了关键路径法,以提高开机率和性能开动率为两条主线,提高设备综合利用效率,从而提高综采产能。
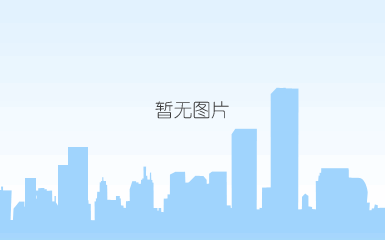
3)提高开机率
►缩短计划维修时间,提高设备开机率:
►精准组织生产,提高设备开机率
►实施tpm管理,降低设备故障率,提高开机率
tpm(全面生产保全活动)是以最大限度地提高设备综合效率为目标,建立贯穿于设备生 命周期,实现设备全员自主维护,将现有设备实现最极限的运用。
a)强化标准化点检作业体系,级三位一体点检和四定标准化作业。
一是形成“三位一体”的点检管理体系。“三位 一体”即岗位工点检、维修工点检、专职点检员巡 检,构筑了设备24小时处于状态受控的点检模式。
二是建立“四定”点检标准化作业机制。
►一是定人,每台设备由谁负责;
►二是定标准,明 确每一台设备点检内容及点检项的标准;ü三是定周 期,不同设备的点检项目定不同周期(日检、周检、 月检);ü四是定流程,定出点检作业和点检结果的处理程序。
b)建立了设备故障分析模式
通过对mes系统中设备运行数据整理分 析,按照故障类型进行分类,对影响设备 故障率偏高的原因进行分析,有针对性的 做设备维护保养,指导设备检修。
c)完善设备预防性维修体系
应用eam系统功能,建立综采及主运设 备现状诊断模型,通过对设备过煤量、历 史大修次数、大型部件及易损件更换频次 等各项指标做现状分析,指导设备科学检 修。
d)规范化操作,降低故障率
►梳理优化流程586个,通过流程标 准化,以图表结合的形式,直观、详细地规定了操作步骤,所需工具,标准方 法,重要参数等,规范员工日常操作行为,降低人为因素造成的设备故障,提高工作效率。
►标准检修流程463个;标准生产工艺流程56个;标准业务流程67个
4)提高负荷率
►优化主运输系统“开、停”顺序,缩短空转待机时间,通过优化每天可以增加18分钟的运转时间,减少27分钟的空转时间。
►合理控制煤机速度,提高产能
根据地质条件、工作面位置等因素的不同,动态调整割煤机速度,解决由于煤量不均造 成压死三机及皮带等非生产性影响因素,减少故障停机时间,从而提高产能。
5)取得的成效
通过以提高设备综合效率oee为主要手段的一系列措施实施,综采较2010年增加实际作业生产时间468小时,可多产煤80多万吨。目前综采oee较2010年提升8.51%;产能较2010年提升10.5%;
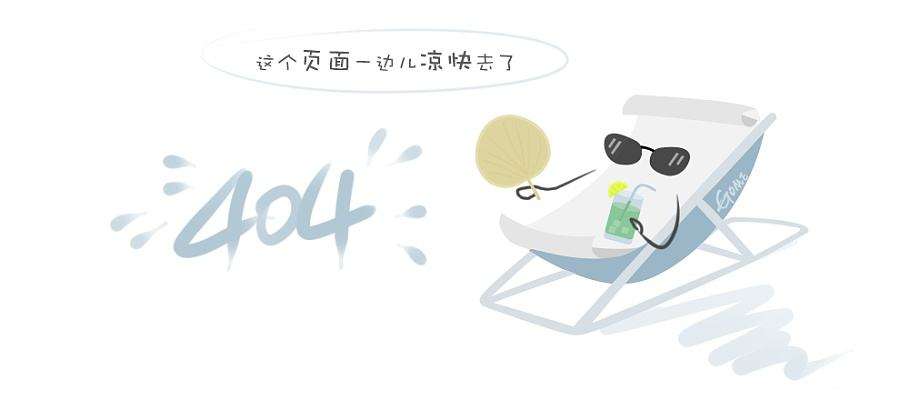
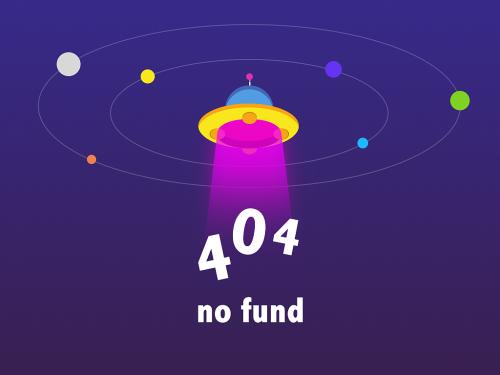
三、连采效率提升
1)项目推进思路结构图:
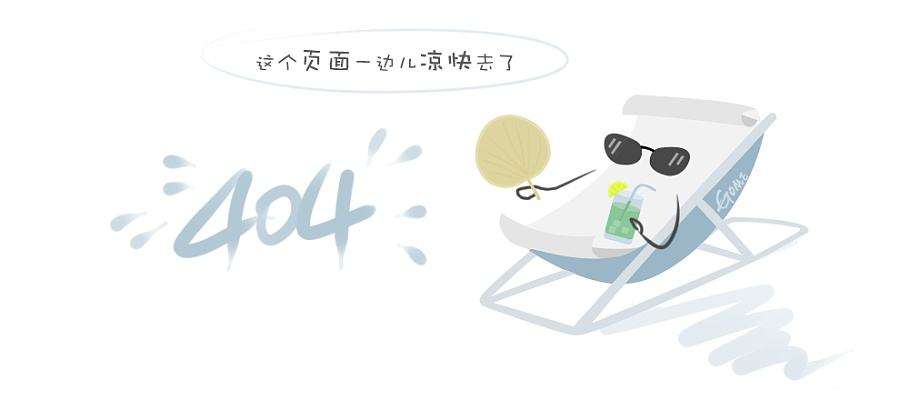
2)提高开机率:
►实施“3 x”柔性检修
连采实施“3.5.8”检修方式。有效消除了“过维修、欠维修”的浪费。与精益化之前相比,此检修方式月可节约32小时。
►科学现场跟班检查,减少非设备停机时间
♦改进前:正常情况下每班安排矿领导、机关跟班、安监员(每班两个安监员)、瓦 检员对工作面生产情况进行6次检查(每班安监员、瓦检员各检查2次),每次检查时间 约为5分钟,造成工作面连采设备6次停机,造成每班影响30分钟,每日60分钟,每月 1800分钟。
♦改进后:矿领导与安监员一组、机关与安监一组、瓦检员一组。实现每班进入工作 面次数降低到4次(检查频次未减少),缩短停机2次。每班增加生产时间10分钟,每日 20分钟,每月增加生产时间为10小时。
►降低设备故障率,缩短设备故障处理时间
♦建立设备24小时点检作业机制。
♦做到班班有人点检,任务明确, 实现检修班检修工点检,生产班岗位工/操作工点检,使设备24小时内处于受控状态,做到及时发现隐 患及时处理,确保设备故障消灭在萌芽状态。
♦建立设备故障分析图表
通过对连采后配套设备故障按 照机械、电气、液压等故障类型 进行分类统计,进行月度分析总 结,有针对性的制定检修计划,为科学检修做精确指导ü建立设备预防维修体系应用eam系统功能,建立连采设 备现状诊断模型,通过对设备过煤 量、历史大修次数、大型部件及易 损件更换频次等各项指标做现状分析,指导设备科学检修。
►完善特殊地质条件的预案,科学支护,提高效率根据不同地质条件,通过合理控制循环进度,科学支护,降低处理顶板冒落严重程度,从而提高设备开机率,进而降低后续工程量(吊伪顶等)及成本。
3)提高掘进效率:
►合理确定循环进度,提高掘进效率;
►合理确定联巷距离:实现连采机割煤能力和梭车运输能力的最佳匹配,总耗时最短;
►软底条件下割煤方式:沿底、沿顶板、沿煤层中间;连续采煤机掘进过程中,遇到软底,严重影响掘进效率的情况下,必须留有500mm以上的煤底时,才能保证正常掘进。并要考虑以下几种情况:
♦沿底掘进:采用快速掘进方式,减少连采设备对底板的破坏程度;在顶板完好情 况下,放大循环进度;
♦沿顶板掘进:采用留设底煤(大于等于500mm),保证巷道底板的完整性;加强顶板支护强度;
♦沿煤层中间掘进:采用留设顶、底煤方式,一般顶、底煤大于等于500mm;若顶、 底煤小于500mm,根据现场实际情况采用沿顶或沿底掘进;
♦不同条件下合理采用风钻、水钻进行支护,提高支护效率
►机制保障,提高生产组织效率--实行连采掘进目标定额管理针对地质条件、循环进度、支护方式的不同,确定不同的分值和单价,工资足额兑现,充分调动区队和员工的劳动积极性,提高了组织效率和掘进效率。
4)取得的成效
通过创新连采作业机制等一系列措施实施,连采较10年增加实际作业生产时间582小时,相当于增加24天生产时间。每支连采队全年可多掘进1000米以上。同等条件下以连采二队为例,2012年与2010年相比预计多掘进3000米
详询021-62373515了解更多信息……
作者:博革咨询